Microchannel-Based Endothelialization of Synthetic Vascular Graft
Patients suffering from cardiovascular disease often present with occlusion of blood vessels due to thrombosis, stenosis or other mechanisms which requires intervention to restore perfusion to tissues. For this purpose vascular grafts are deployed to bypass these occluded regions. Particularly in small diameter vessels (<6mm diameter), autologous vascular grafts are currently considered the gold standard. There are, however, cases where these vessels are not available due to previous harvest or patient co-morbidities. In such cases, synthetic vascular grafts may serve as a promising alternate treatment, but current systems suffer certain failures. Due to the interaction of these synthetic materials with the blood and the physiologic wall shear stress conditions present in small diameter vessels, thrombosis and stenosis are common. In order to remedy this failure, the CARE Lab is working with the LaDisa Lab to develop a novel microchannel patterned synthetic vascular graft capable of maintaining endothelial adhesion under physiologic wall shear stress and therefore reducing the risk of thrombosis and stenosis seen in other grafts.
To create this novel vascular graft, iterative CFD modeling and 3D printing has been implemented to create microchannels within an electrospun polyurethane graft material. Endothelial cells have been cultured and seeded on these stamped surfaces before being exposed to physiologic wall shear stress using a parallel plate flow chamber. Initial trials indicate a promising increase in retention within these stamped microchannels and efforts are underway to optimize channel geometry for improved function while working toward in vivo applications.
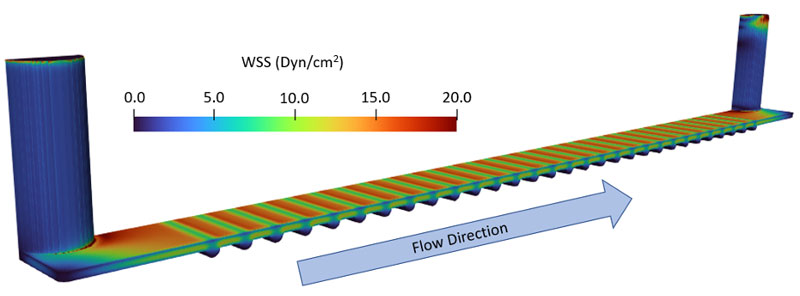
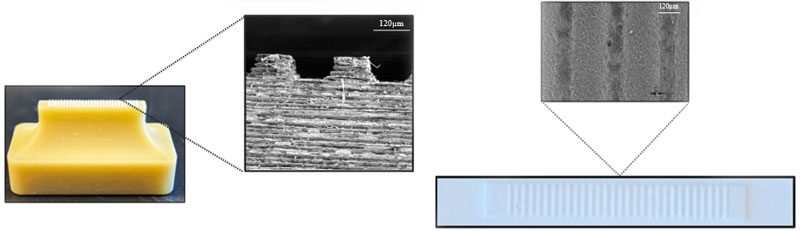
Image Descriptions
Top: Parallel plate chamber based CFD simulation with distributions of WSS. WSS is reduced to <1 dyn/cm2 within stamped channels compared to 15 dyn/cm2 atop the surface between the channels.
Bottom Left and Right: SEM Imaging side profile of 3D printed stamp (left) and the imprint it produces in electrospun polyurethane (right).
Project Lead
Alexander Armstrong
Research Technologist
Medical College of Wisconsin
View more CaRE Lab Research